In our Fabricator General series, we talk about hobbying techniques and tricks, and ways to build, model, shape, and fix everything, with an eye toward information for both beginners and veterans. This week, Charlie Anderton, James “Boon” Kelling, Kevin Genson, and Chris “head58” Tatro talk about how to build your own carrying case.
Charlie’s Carrying Case
I made this case about a year and a half ago. At the time, I was needing something, anything, to transport my miniatures from my home to the game store. I had just recently started going to more stores and events to play, and the thought of throwing all my models in a shoebox scared me to death. I had researched alternatives and while I had found something like the A-Case it was way more than what I wanted to pay. The premise of it though, installing magnets on the bottom of each miniature and then placing all your models on metal sheets within a case, appealed to me. With a bit more research, I decided to try and build my own. I’ll list the steps I actually took in making this case, approximate cost, links to similar parts found online, and include things I would have done differently. Hopefully, if I had a guide like this, the case would have come out perfectly – as it stands, it’s a very functional, decent case.
It hopefully goes without saying, but I’ll say it anyway – be safe. Wear protective gear. Don’t cut off appendages. Don’t be a dumbass.
Materials:
- Toolbox
- Sheet metal
- Magnets
- Method to fix metal inside the toolbox (screws, nuts, and washers shown below)*
The toolbox needs a flat or fairly flat base inside in order to fix the metal to it securely. It’s also helpful if it has an upper shelf like is shown above. This allows for multiple levels of model storage, plus a place to store dice, rulers, objective markers, etc.
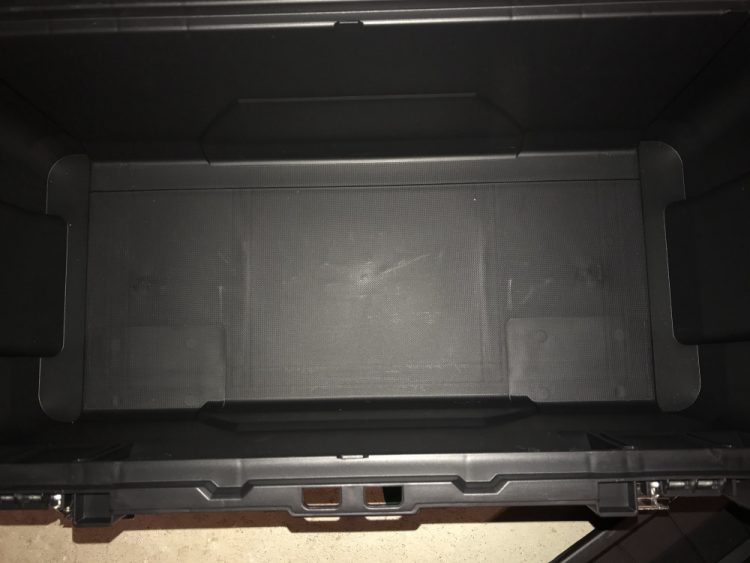
The sheet metal was pretty thin, though I don’t remember the exact thickness. It’s ok if it’s a little flimsy because you’re going to have to be cutting through it, so don’t try to find 1/8″ thick or anything.
The magnets that you’re looking for should be able to fit under each base. I found neodymium 3/8″ diameter magnets to work well and be surprisingly strong. This shows the scale for reference.
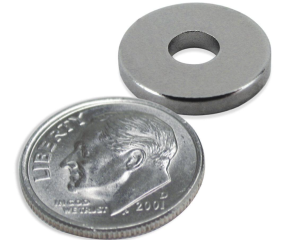
*I originally thought I’d drill through the sheet metal and bottom of the toolbox and fix the metal to the bottom using screws, nuts, and washers. However, I started questioning just how easy it would be to drill through the metal with my handheld drill, and ultimately, due to the flatness of the inside of my box, elected to just use really strong double-sided sticky tape. Screws would have done the job too, but if you’re unable to do that (or don’t want to) know that strong tape works just as well.
All in all, materials cost me under $30 for the toolbox, metal, and strong tape. Then I bought as many magnets as I needed, which for me was about 60, so another $12 dollars for a total of less than $50. That’s somewhere between a half and a third of the equivalent A-Case.
Tools:
- Straight edge
- Marker
- Tin snips
- Tape measurer
- Drill and bits (if not using tape)
- Metal file (not shown)
- Superglue (not shown, but you probably already have some of this from model assembly)
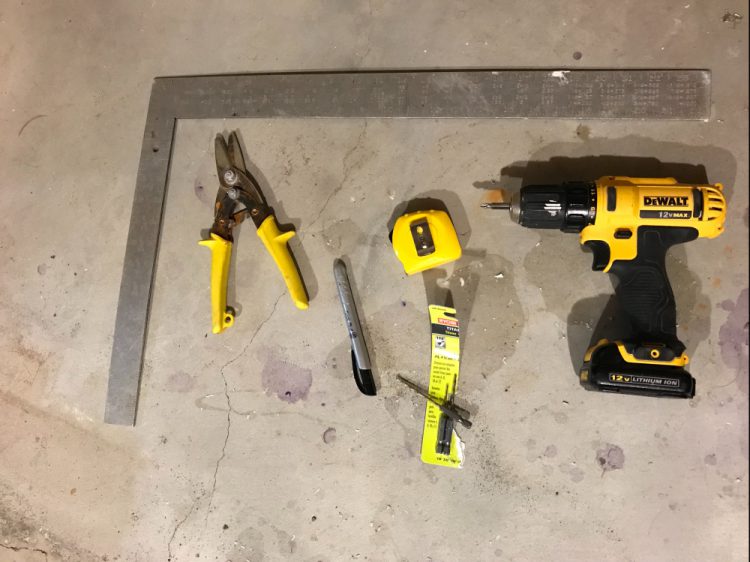
Steps:
- Measure the inside of your toolbox in both directions. Subtract a half-inch from each measurement. This subtraction will ensure that you have a little wiggle room later on.
- Use the straight edge, marker, and tape measure to mark a piece of sheet metal to the resultant dimension from step #1.
One side cut, one to go. - Using the tin snips, carefully cut the metal to the desired dimensions. Wear all necessary protective gear to ensure that you stay safe and generally, don’t be a dumbass.
- File down any sharp edges or corners from the metal using the metal file. Get rid of these sharp edges carefully! Don’t cut yourself!
- If using tape, apply tape to one side of the cut metal. If using screws, position the metal sheet inside the box, mark the desired locations of the screws, position the toolbox above something that you can drill into or such that you have clearance underneath it, and drill each hole.
- Affix the metal to the bottom of the box using the tape or with the screws, nuts, and washers.
- Glue a magnet (with strong super glue) to the inside bottom of each model that you want to use with this case. Bases with slots might present problems, but most other bases should have some recess under the base that provides clearance for the magnets. All of my infantry bases had already be weighted by gluing pennies in the underside, so I had a bit less clearance than most. Even still, I had just enough room to fit the penny and magnets under the base will little to no clearance issues.
You’re done! It’s really that simple. Make sure to wait for the glue to thoroughly dry because you don’t want to get too eager to test the magnets and then pull off the still-wet super glue. You could fix a piece of sheet metal to both the inside bottom and the upper layer of the toolbox to provide maximum transporting space, but the bottom was enough for the army I was taking, so I just left the top caddy free and clear of sheet metal. I can always go back and put metal there if I need the space. For now, it’ll function as an area to hold dice, rulers, etc.
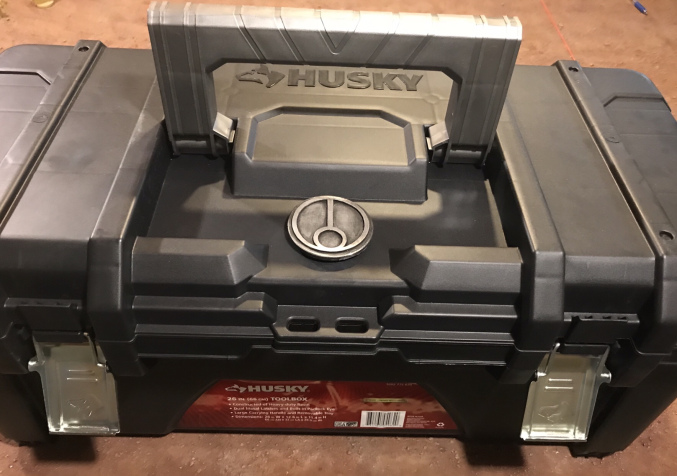
What I would have done differently:
- I would have looked for an alternative style of the magnet for my bases with slots in them. The magnet doesn’t sit flush with the bottom of the base so it makes the model a tad wobbly and this is even more true of the clear flight stand bases that drones use. Placing the magnet in the center of the base helps, but it’s not perfect.
- The size of the toolbox itself is a little large. It’s got enough room for most of my army lists, but I think I would prefer two flights of storage for models, rather than one large one.
Looking back on this now, one and a half years later, I can say that this has done everything I’ve needed it to. It’s a little larger than I care for (it doesn’t fit on the top of my tournament pushcart, for example) and I want to make a new one in the future.
head58’s Adeptus Titanicus Case
Like Charlie, I knew I needed something better than a cardboard box to store and transport my Adeptus Titanicus models, but I’m not smart enough to navigate the KR Multicase site. Instead, I decided on a plastic box with some kind of magnetic bottom to keep them from smashing into bits. I spent a lot of time in hardware and craft stores looking for a plastic bin that was tall enough to accommodate a Warlord (about 5 ¾” or 15cm) and spacious enough to hold whatever models I ended up buying (way too many) but didn’t want a laundry hamper. None of the multitudes of models of Really Useful Boxes, even ones I’d have to import from another country, were exactly what I wanted. Eventually, I stumbled onto a 19-quart clear storage box from an outfit with the confidence-building all-caps name of IRIS USA, and it was just what I was looking for – about 7” (17.7cm) tall and 11.5” x14.5” (29.2xm x 36.8cm) on the bottom of the box. That bottom of the box interior dimension is crucial because most of these plastic storage bins slope inward from the top, and the dimensions listed on the sticker or website are usually those at the top, which doesn’t help you to know how many warmans you can stand in the thing.
After securing the box, I went back to the hardware store and bought some thin steel sheets. Steel, not aluminum, since magnets won’t stick to aluminum. There’s no way I made that mistake and had to go back for a different material, nope. A pair of heavy snips later I had the sheet sized correctly to fit the bottom of my box.
To secure the nice, ferrous steel plate to the bottom of the box I used heavy duty double sided tape rather than just glue. Even though the steel sheet was thin it was reasonably heavy and I wasn’t sure I trusted glue to hold it down. Gorilla double sided mounting tape did the trick just fine.
Preparing the models themselves was the easy part. I found some strong neodymium magnets that fit under the bases and superglued them in. That part is probably the weakest link in the storage and I worry about the glue letting go and my models tumbling around as if they were in the clothes dryer, but I also worry about things like asteroid strikes and supervolcanoes and those are also fairly unlikely events.
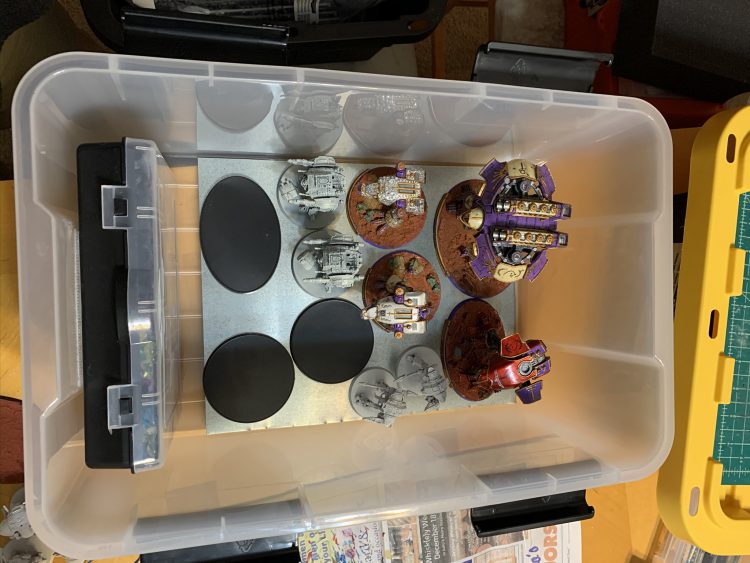
The last step, if I wanted this to be a self-contained transport solution, was a way to hold my dice and all the magnetized weapon loadouts for my Titans. I picked up a small hardware storage box that would suffice and puzzled with how to attach it. Currently, it is attached to one end of the box interior with velcro strips, but I’m having issues with the glue holding the velcro to the side of the larger box (see!) so I’ll likely rip that all out and replace it with magnets at some point.
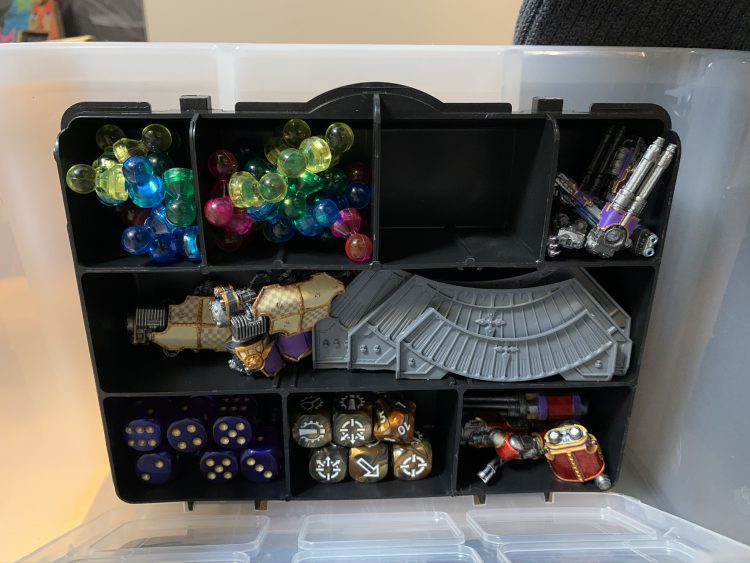
Ideally, I would also have a way to keep the rulebook, measurement templates, cards, and control terminals inside the box as well. I have about 2” (5cm) between the inside of the lid and the tallest point of my Warlord Titan so maybe something can be secured there.
In a related but non-Ham-adjacent storage tale, I used a similar method for storing and transporting my Butcher’s Guild team for Guild Ball. A metal lunchbox is plenty big to carry the number of models needed for that game, and would probably work for Kill Team, Blood Bowl, Necromunda or any other smaller skirmish game.
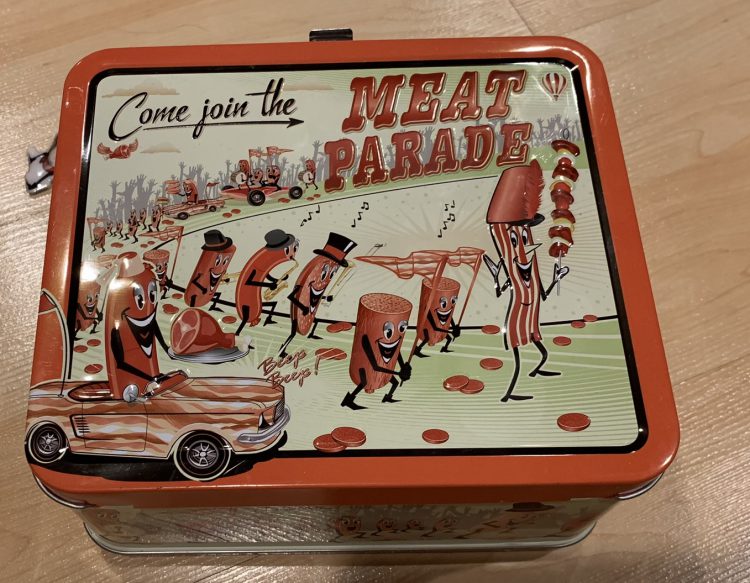
Boon’s Carrying Case(s)
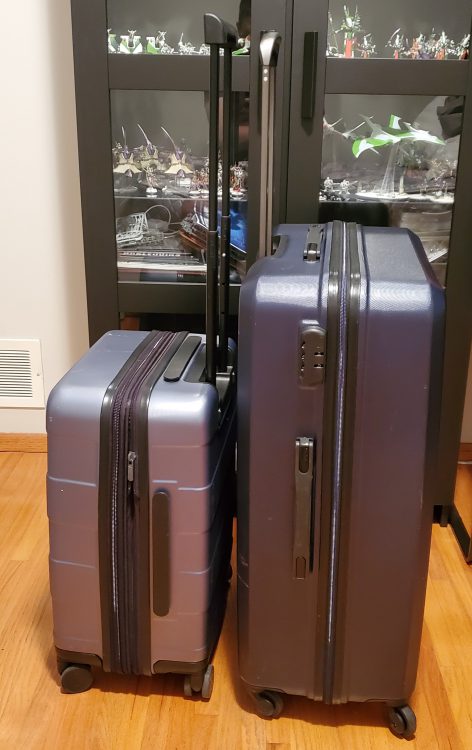
Why Did I Build These?
I built both of these ahead of LVO last year as a way to safely and efficiently transport my models. I had considered some of the commercial alternatives out there on the market, but frankly, I didn’t know enough about them and I didn’t like the foam cutouts I’d seen at various cons. So I said “fuck it, I can make one” and did.
I made them to fly with to various events around the country. That means the requirement was that they’d need to protect my models after being manhandled into checked luggage. For that reason, I chose a hardcover suitcase that wouldn’t easily give to puncture or drops. So I got a large one for large models and vehicles, then a smaller carry-on for infantry, bikes, characters, etc that I can keep close.
What I like about this case is that at any time I can easily replace or repurpose the foam to meet my current needs. More vehicles? No problem, just build more modular foam inserts. As you can see below, the large case fits three planes (on stands) as well as 6 vehicles and more in the unused corner. In reality, I often bubblewrap other items and then fit them into the vehicle slots. The bubble wrap is key for the large cutouts as you want to minimize movement of models and the bubble wrap happens to provide a perfect cushion without compressing the model and creating stress points that snap small parts.
Materials and Cost
So what do you need? Well, depending on how much stuff you want to carry, and what types of models, you’ll need to size your case appropriately. It’s not a requirement, but both 360-degree spin wheels and a retractable handle on the suitcases I’ve found to be critical to easily move – it’s super convenient. Recommend 100%. You can grab a suitcase wherever you find a good deal, I went with Amazon because of the ease of variety – though if you have a hard time imagining the dimensions of the case head on down to your nearest Target, Wal-mart, or whatever store and take a look at what the sizes represented.
Materials:
- Hardcover suitcase
- Knife
- Scissors
- 1” Thick Upholstery Padding Foam Sheet
- Sharpie Marker
- Gorilla Glue or Similar
- Bubble Cushioning (Packing Material)
All told, a suitcase, foam, and glue will likely run between $120-180 depending on how big of a suitcase and how much foam you need.
How to Build
Step 1: Gut the Case
You want to make as much room for sweet, sweet plastic crack as possible – hardcover cases come with a liner and more webbing – cut all this out making sure to not cut any connective straps between the two sides.
Step 2: Line the Top and Bottom
This is more of an option, but I like to take one layer, and encase the inside of the top and inside of the bottom to fit and ensure a snug fit. This means measuring the interior, gutted dimensions, including the curvature at the corners, and marking and cutting your foam to fit. If you went gucci and bought a case with a retractable handle it will rest approximately 1” off the bottom case, cutting three pieces to fit that gaps here will help your actual layers to sit properly and snugly (it’s important that they remain snug).
Step 3: Establish How Many Layers Can Fit
This is where you plan out your layout. Each layer of foam is 1” and each level will be at minimum 2” (bottom layer and the cutout layer). So if you have larger mini’s it may make sense to make one level of infantry where each model lies in a 1” cutout and a second layer of larger models that need a 2-3” cutout. Alternatively, you may want to make modular sections as necessary (see my large suitcase). It just depends on your specific needs.
Step 4: Cut out Layers and Lay Out Models
Now you need to cut the individual 1” layers that will fill your case – remember the snugger the fit the less your models will jostle around. Once you have your planned layout, lay down your models on the layers you want as cutouts – mark the sizes with your sharpie. You may want to add extra slots if you have space – it will come in handy later because you won’t be able to add them easily once you’ve put this together.
Step 5: Cut the Marked Areas and Glue the Levels Together
Once you’ve marked them out, use a knife or scissors to cut out the slots – it’s tedious. With each layer completed, glue them together with the gorilla glue and use heavy objects to compress the layers together. I generally lay them on the ground and then use heavy books for at least an hour or two.
Once you have all the layers cut and glued, layer them back in your case and test the fit, voila!
Additional Notes:
I use some bubble wrap to fit any extra space above larger models (not the infantry, they’re fine) but things like tanks and bikes are hard to fit into a snug fit and will jostle around a lot more. The bubble wrap will prevent them from being damaged – just be sure not to tightly wrap it around things like an antenna, etc.
Kevin’s Magnetic Sheeting Cases
When I had first heard about using cases with magnets like Charlie, I was a little worried about the magnets sticking the models together on the battlefield. I had also had a lot of success weighting down the bases of my models so that they were less likely to be wobbly. I ended up taking a slightly different approach; instead of putting magnets on the models and using metal sheeting in the case, I used metal washers in the model and magnetic sheeting in the base. The nice thing about this approach is that it’s extremely flexible. The magnetic sheeting can be cut with scissors and is already backed with adhesive. You can fit it to any size you want. The example below uses a plastic case I found online with removable shelves (the top levels can hold two Knights, the bottom two Armigers), but it would work just as easily with other cases. In fact I would recommend not using such a tall case, as it can easily tip over.
Materials
- Adhesive Back Magnetic Sheeting, 1/16″ Thick (McMaster-Carr Part No 5756K56)
- Suitable Container (Double Deep Super Satchel, US Plastics Part Number 56682)
- Steel Inserts (1″ Washers for #10 Screws, McMaster-Carr Part Number 91090A120)
That’s it. All you have to do is cut the sheeting to size, stick in inside the case, and put your models on top. If you’re concerned about the models moving you can use 1/8″ thick sheeting instead. The 1″ washers fit perfectly in 32mm bases when double stacked. Smaller washers will fit in smaller bases, or you could experiment with a mixture of metal filings and adhesive to get a magnetic (and heavy) filling for bases with slots or odd geometry. For larger bases you can add multiple washers as seen below.
I would not recommend using this solution for traveling via air, nor would I suggest inverting the models (they’ll stay stuck to the magnets but can be dislodged if bumped). This approach can also easily be applied to a display board; simply apply the magnetic sheeting to the bottom of the board and then prime and texture as needed.
Thanks guys! If you have any questions about the methods described here, or if you’ve made your own carrying case and want to share your One Weird Trick, then comment below, hit us up on Facebook, or e-mail us at contact@goonhammer.com.